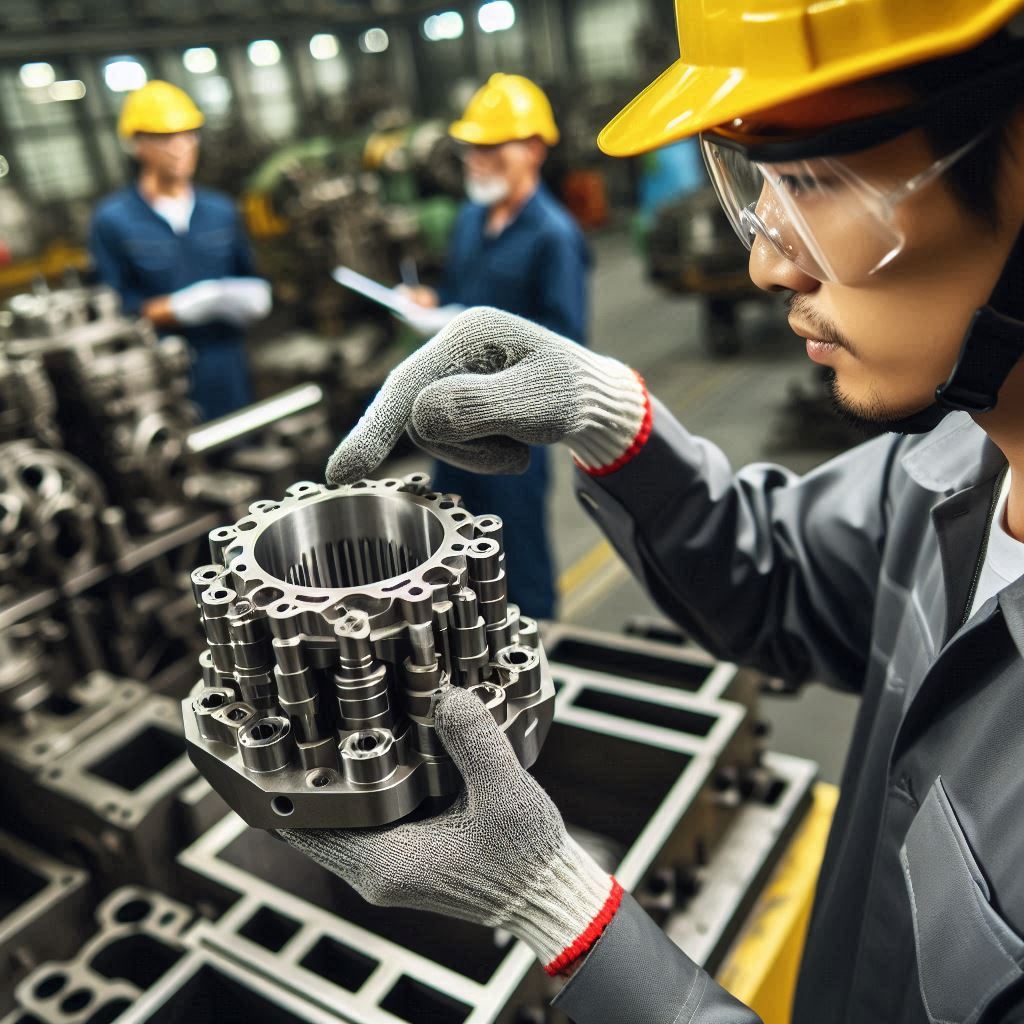
Tolerances in machined investment castings are critical for ensuring that components meet precise dimensional and functional requirements, especially in industries like aerospace, automotive, and medical devices. Investment casting inherently offers near-net-shape components with tight tolerances, often around ±0.005 inch per inch, reducing the need for extensive machining. However, when additional precision is required, secondary machining processes are used to achieve even finer tolerances—sometimes as tight as ±0.001 inch. Engineers must consider factors such as material shrinkage, casting complexity, and surface finish requirements when specifying tolerances. Understanding the balance between casting precision and post-casting machining helps in optimizing design, reducing costs, and ensuring reliable part performance.
Machined Investment Castings for the Aerospace Industry: Key Advantages
Machined investment casting offer significant advantages for the aerospace industry, where precision, strength, and weight optimization are critical. This manufacturing process allows for the production of complex, lightweight components with excellent dimensional accuracy and superior surface finish, reducing the need for excessive machining. Aerospace-grade alloys such as stainless steel, titanium, and nickel-based superalloys can be used to meet the industry’s demanding performance and temperature resistance requirements. With secondary machining, cast components achieve the tight tolerances essential for flight-critical parts like turbine blades, structural brackets, and fuel system components. Additionally, the repeatability and consistency of machined investment castings ensure high reliability, making them a preferred solution for aerospace OEMs focused on safety, performance, and regulatory compliance.
High-Performance Machined Castings for Defense and Industrial Applications
High-performance machined castings play a vital role in defense and industrial applications where durability, precision, and reliability are non-negotiable. These castings are manufactured using advanced investment casting techniques followed by precision machining to meet stringent specifications and withstand extreme conditions such as high stress, corrosion, and temperature fluctuations. Materials like stainless steel, titanium alloys, and nickel-based superalloys are commonly used to ensure strength and longevity. In defense, machined castings are essential for components in weapons systems, armored vehicles, and aerospace defense equipment, while in industrial sectors they are crucial for pumps, valves, compressors, and heavy machinery. The combination of casting complexity and machining precision allows manufacturers to deliver components that offer superior performance, reduced weight, and enhanced operational safety.
Precision Machined Investment Castings from India: Quality Meets Affordability
Precision machined investment castings from India offer an ideal blend of high quality and cost-effectiveness, making the country a preferred destination for global manufacturers. Indian foundries leverage advanced casting technologies combined with skilled machining expertise to deliver components that meet stringent international standards while maintaining competitive pricing. This affordability does not come at the expense of quality; rigorous quality control processes, certifications, and the use of premium alloys ensure that every casting achieves precise dimensions, excellent surface finish, and reliable performance. As a result, industries ranging from automotive and aerospace to medical and oil & gas increasingly rely on Indian precision machined investment castings for scalable production without compromising on durability or accuracy.