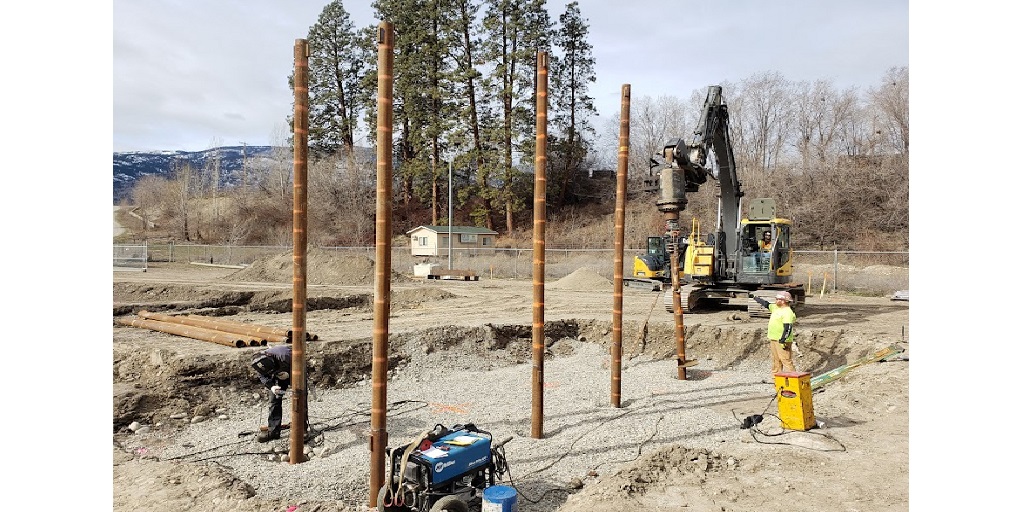
Helical piles are known for their efficiency, ease of installation, and load-bearing strength. But like any engineered system, failures can still occur when proper protocols aren’t followed. From soil miscalculations to installation oversights, these failures are rarely the fault of the product and more often the result of human error or environmental misjudgment. If you’re exploring BC helical piles for your project, here’s what you need to know about common causes of failure—and how to avoid them from the start.
Inadequate Soil Investigation
One of the leading causes of helical pile failure is poor or incomplete soil analysis. If the soil profile isn’t properly assessed before installation, there’s a high risk of selecting the wrong pile length, shaft size, or even installation method. For example, highly organic or loose soils may offer little resistance, causing the piles to shift under load.
How to Prevent It:
A thorough geotechnical investigation is essential before any pile installation. Soil conditions can vary greatly, especially across different regions in BC. Helical piles must be selected based on torque correlation to the actual soil strength at depth. Never skip the step of reviewing a full soil report before proceeding.
Improper Torque Monitoring
Torque is a direct indicator of the pile’s capacity. If installers don’t monitor or record the installation torque properly—or worse, guess the numbers—the pile may not reach the designed capacity. This can result in pile movement, settlement, or even complete structural failure over time.
How to Prevent It:
Work only with qualified installers who use real-time torque monitoring equipment. Logs should be kept for each pile, verifying that minimum torque and depth requirements were met. A detailed torque report is not just good practice—it’s your insurance against premature failure.
Underestimating Lateral Loads
Helical piles excel at vertical load-bearing, but lateral forces—such as wind loads on tall structures or seismic forces—can become problematic if not accounted for. Piles may start to tilt, especially in looser soils where lateral resistance is already limited.
How to Prevent It:
Make sure lateral load calculations are part of the structural design. If needed, helical piles can be paired with concrete grade beams or reinforced caps to increase lateral stability. Engineers may also recommend deeper embedment or the use of larger shaft diameters to handle such stresses.
Installation in Frozen or Oversaturated Soil
BC’s varied climate means some projects will encounter frozen ground or water-logged soils. Installing helical piles in these conditions can lead to premature refusal, inaccurate torque readings, or long-term movement as the soil thaws or dries.
How to Prevent It:
Schedule pile installation during stable ground conditions whenever possible. If installation must proceed during winter or wet seasons, soil heaters, casing, or dewatering techniques should be employed to improve accuracy and effectiveness.
Use of Incompatible Materials
Corrosion is another slow-moving cause of helical pile failure. When the steel pile is not properly galvanized or otherwise protected, prolonged exposure to moisture and soil acidity can deteriorate the metal over time, especially in coastal or clay-heavy regions of BC.
How to Prevent It:
Choose BC helical piles with proper galvanization or epoxy coatings rated for local environmental conditions. Additionally, cathodic protection can be implemented for highly corrosive soils. Always request material specifications and coating certifications before installation.
Helical pile failures are preventable. With proper design, torque monitoring, and expert installation, your foundation can last decades. Knowing the unique demands of BC helical piles is key to avoiding costly repairs.
For more information about Drilling Company Okanagan Valley and Underpinning Services Bc Please visit: ATLAS PILING.