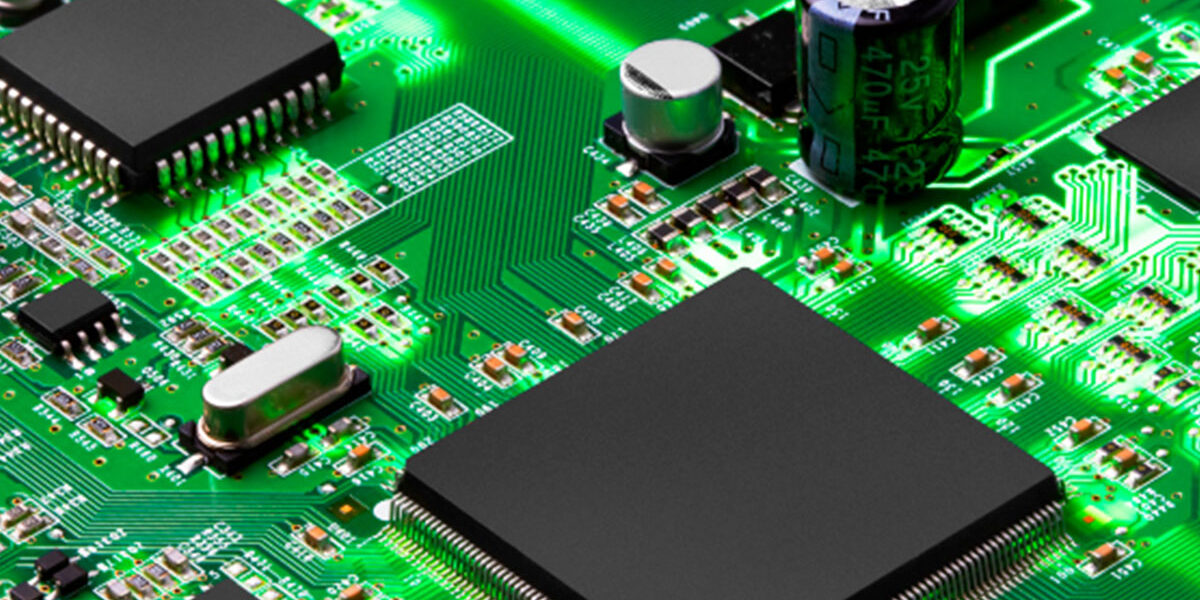
In the fast-paced world of electronics manufacturing, Surface Mount Technology (SMT) has revolutionized how printed circuit boards (PCBs) are assembled. Whether you’re a seasoned engineer or just exploring PCB assembly options, understanding SMT is essential. In this guide, we’ll cover everything you need to know about SMT in the PCB industry—from its basics to the benefits, applications, and how it compares to traditional methods.
What is SMT in PCB?
Surface Mount Technology (SMT) is a method of mounting electronic components directly onto the surface of a PCB. Unlike the older through-hole technique, SMT does not require drilling holes through the board. Components used in SMT are called Surface Mount Devices (SMDs), and they are typically smaller, faster to place, and more cost-effective.
How SMT Works
The SMT process involves several key stages:
- Solder Paste Application – A stencil printer applies solder paste to the PCB’s pads.
- Component Placement – Automated pick-and-place machines place SMDs accurately onto the paste-covered pads.
- Reflow Soldering – The board is heated in a reflow oven, melting the solder and securing the components in place.
- Inspection and Testing – Advanced optical inspection (AOI), X-ray, and functional tests ensure quality and reliability.
Benefits of SMT in PCB Assembly
SMT has become the industry standard for PCB manufacturing because of its numerous advantages:
- Miniaturization: Enables compact designs, ideal for modern electronics.
- Cost-Effective: Reduces labor and material costs.
- Speed: Automated assembly processes increase production speed.
- High Reliability: Better performance in high-vibration or harsh environments.
- Design Flexibility: Supports double-sided PCB assembly with high component density.
SMT vs. Through-Hole Technology
Feature | SMT | Through-Hole |
---|---|---|
Component Size | Smaller | Larger |
Assembly Speed | Faster (automated) | Slower (manual or semi-auto) |
Cost | Lower | Higher |
Strength | Good for light components | Better for heavy-duty parts |
Application | Consumer electronics, wearables | Industrial, aerospace, power |
Applications of SMT
SMT is found in nearly every modern electronic device, including:
- Smartphones and tablets
- Medical devices
- Automotive electronics
- Industrial control systems
- Wearable technology
- Consumer electronics
Challenges in SMT
Despite its advantages, SMT has some challenges:
- Thermal management: Smaller components can overheat easily.
- Design precision: Requires accurate PCB layout and stencil design.
- Inspection complexity: Small size makes visual inspection difficult without advanced tools.
SMT Trends in 2025 and Beyond
As technology advances, SMT continues to evolve. Key trends include:
- Increased automation with AI-assisted placement and inspection.
- Smaller, more complex components such as BGA and QFN packages.
- Eco-friendly soldering techniques to meet RoHS and sustainability goals.
- Integration with Industry 4.0 for smarter, data-driven manufacturing.
Final Thoughts
SMT has become the backbone of modern electronics manufacturing. Its efficiency, scalability, and adaptability make it indispensable in today’s PCB industry. Whether you’re launching a new product or optimizing an existing design, embracing SMT is crucial for staying competitive.